ZOË POWELL CERAMICS
Zoë Powell holds a B.A. in Ceramics and a B.S. in Biology from The College of William & Mary and is currently working as a studio ceramist at Studio Alluvium, a gallery and native clay production studio she co-founded with her partner Mitch Iburg in St. Paul, Minnesota.
Her sculptural work serves as a formal exploration of human emotions; an attempt to visualize the intangible. Zoë is a former wood-fire resident of both the Cub Creek Foundation, in Appomattox, Virginia, and Cobb Mountain Arts and Ecology Project, in Northern California. She is a past VMFA fellowship recipient and has been awarded numerous grants for her work with native clays and wood firing. Her work has been exhibited in various galleries around the country.
Statement
My ceramic sculptures serve as conceptual explorations of human emotions. Themes that work on both the material and ideological scale appeal to me; themes like tension, fragility, and imbalance are especially attractive. I’m concerned with how internal factors, like psychological and physical sickness, influence the body’s external appearance. I have a fascination with biological development and strive to incorporate a feeling of skeletal structure in all my pieces. The figurative additions are abstractions that manifest themselves in small sections of my work, but do not form a whole, traditional figure. I emphasize certain areas with false bones, tendons, and veins to give my sculptures the appearance of gauntness and stress. I find great beauty in underlying structures pushing through to the surface of the skin. In all my work, the clay is finessed and often driven to extreme levels of attenuation.
Many of my sculptures represent two forms pulling away from, or compressing against, each other. They act as metaphors for human relationships that are based on impending separation or forced attachment. Many people find the development of relationships to be a source of anxiety, and I attempt to express this interactive struggle through the physical movement of the clay.
Works available at BOON
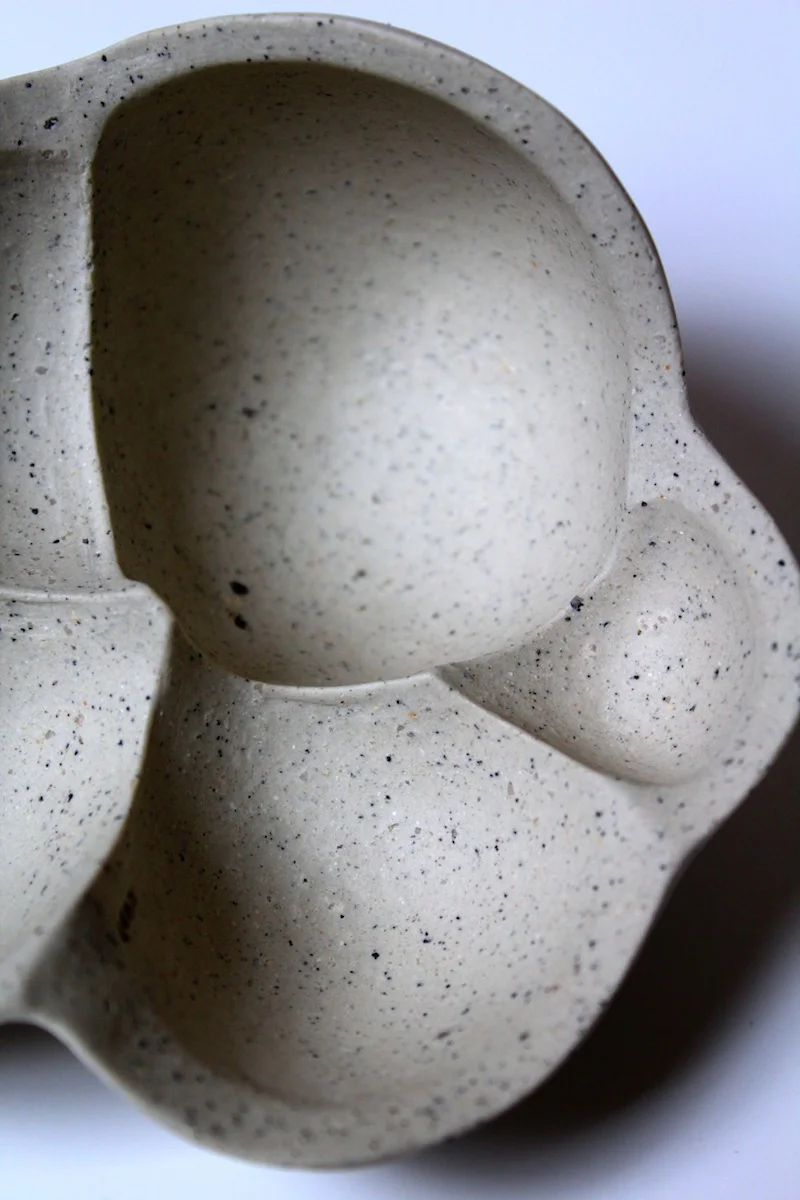
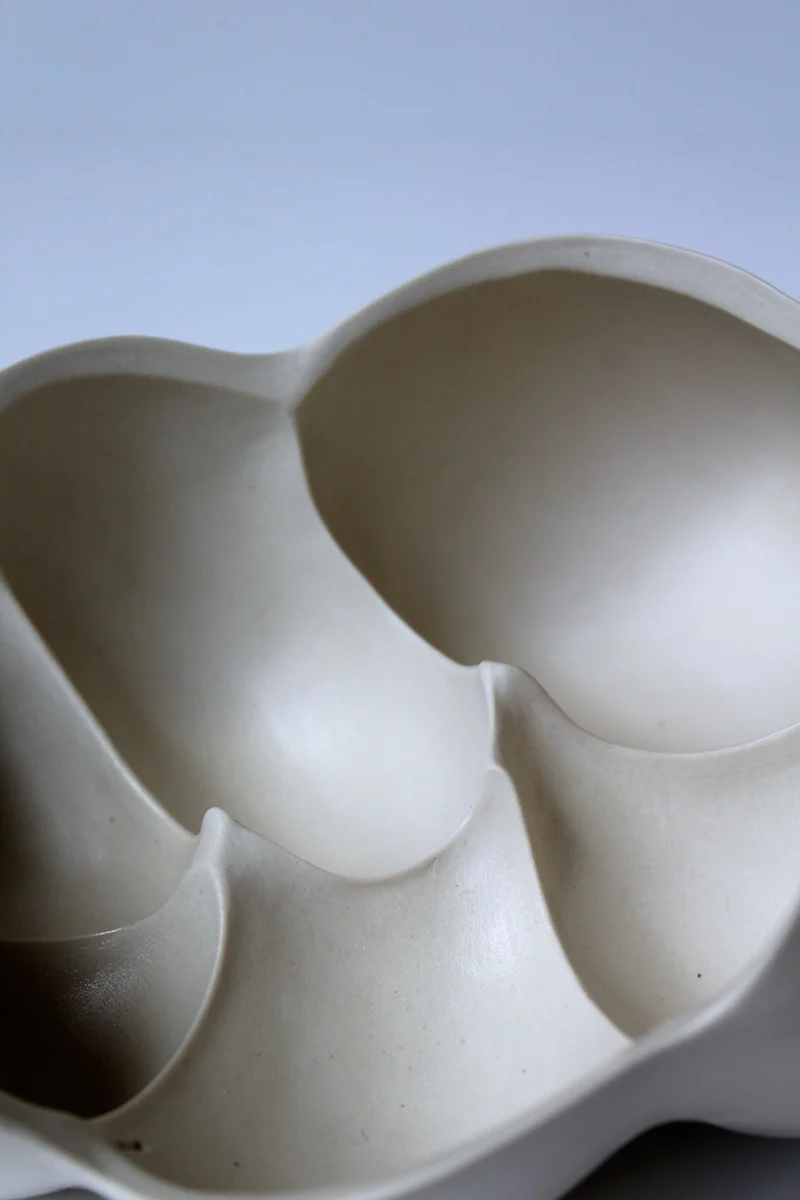
SILK
Material: hand-processed Minnesota brick clay, kaolin, and taconite sand
Firing Method: 2240°F [1227°C], oxidized electric
Finishing Method: wet-polished with 200 grit diamond sandpaper, sealed with a light beeswax varnish
Focus: material
Ideation:
The clay used in this collection naturally fires to a warm, yellow-orange color, without the addition of stain or pigment. Using a clay with such inherently beautiful properties gives me a responsibility to uphold its native characteristics. In an effort to preserve the depth of surface on these works, I do not glaze the exterior. I find that glazing would not only obstruct the appearance of the stones in the clay, it would create a cold, hard gloss that would prove uninviting to the touch. In order to properly honor the allure of the clay, I simply finish the work by polishing the surface to expose the clay’s innate luster. The sheen, texture and color of this polished surface all reference the warm, raw tones of natural silk.
Sinew
Material: porcelain
Firing Method: 2260°F [1238°C], oxidized electric
Finishing Method: wet-polished with 200 grit diamond sandpaper
Focus: form
Ideation:
Creating with porcelain is a way for me to pare my work down to what I find most essential- graceful form. Viewers of my work often see the clay before appreciating the piece itself. While I have a deep respect for raw, hand-processed materials, I find that working with pure porcelain is like working with a blank canvas free from other distractions. With this collection, I want my work to be perceived as intrinsically compelling because of my forms- not necessarily because of the material from which it is made. This collection includes work made with pure, hand-polished porcelain, work made with pure porcelain that has been lightly clear-glazed, and work made with a raw porcelain derived from foraged clays and minerals. The name sinew alludes to this collection’s feeling of strength, connectivity and delicacy.
sinter
Material: hand-processed Minnesota ball clay, kaolin, and silica
Firing Method: up to 2300°F [1260°C], reduced woodfire
Finishing Method: lightly sanded with 200 grit diamond sandpaper, sealed with mineral oil
Focus: surface
Ideation:
Woodfiring has been revered for hundreds years for its often unpredictable results. There are many variables that can affect the outcome of woodfired ceramics, but I try to curate these variables to gain as much control of the process as possible. When loading, I aim to place my work in the coolest areas of the kiln; areas that see more flame movement and ember contact. I strive for matte surfaces and warm to black tones on my work, but sometimes also encourage charcoal buildup for a mossy green-blue texture. Using locally sourced clays in the wood kiln adds another layer of intensity to the work. The naturally occurring stones melt at different temperatures and interact with the flame and ash in unique ways.
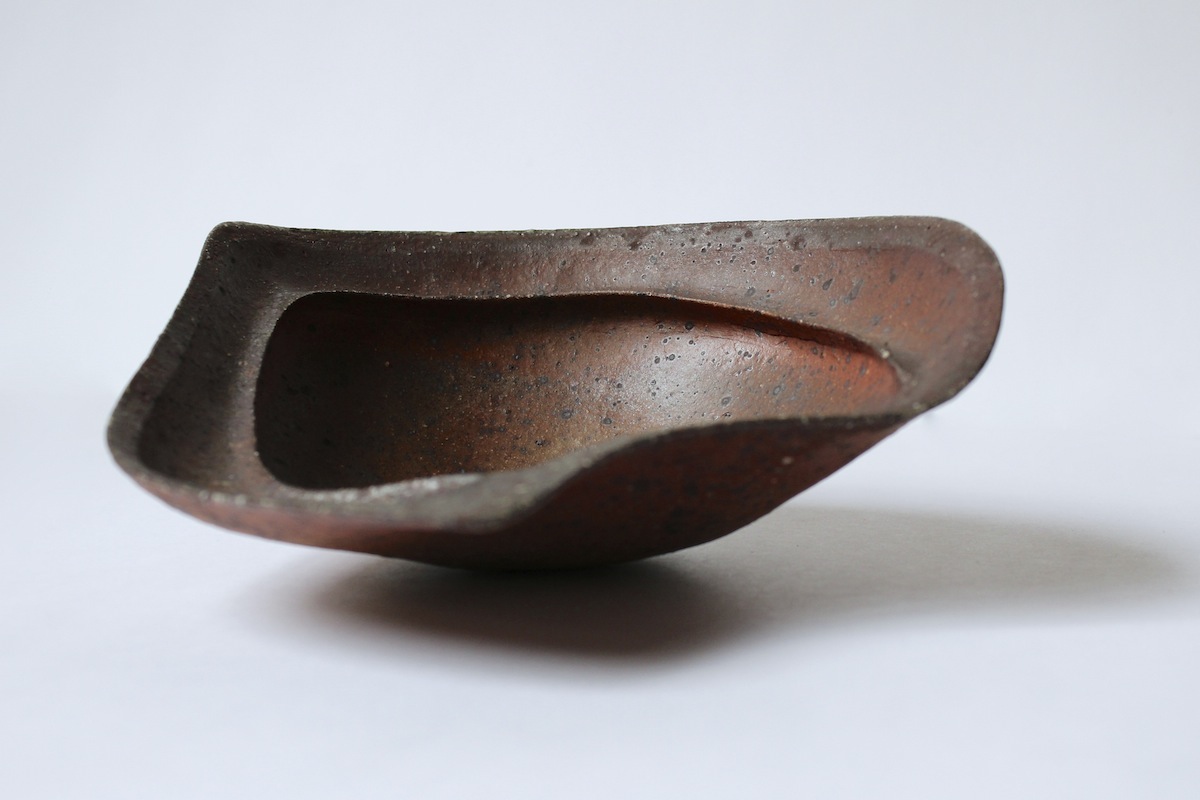