
POPPY LAWMAN
Poppy Lawman is a newly established designer based in Oslo, Norway. Lawman studied a Masters in Product Design from Oslo Metropolitan University and her design practice focuses on transparent process, locality, form, and emotional design. In 2019 she was the recipient of the prize “The Years Newcomer” from the Bo Bedre Design Prizes and in 2020 participated in Norwegian Presence’ international exhibition “Innovation In Process”.
BUE - brush series
Oak, beeswaxed linen, and coco fiber. Mixed Dimensions, Made in Oslo, Norway
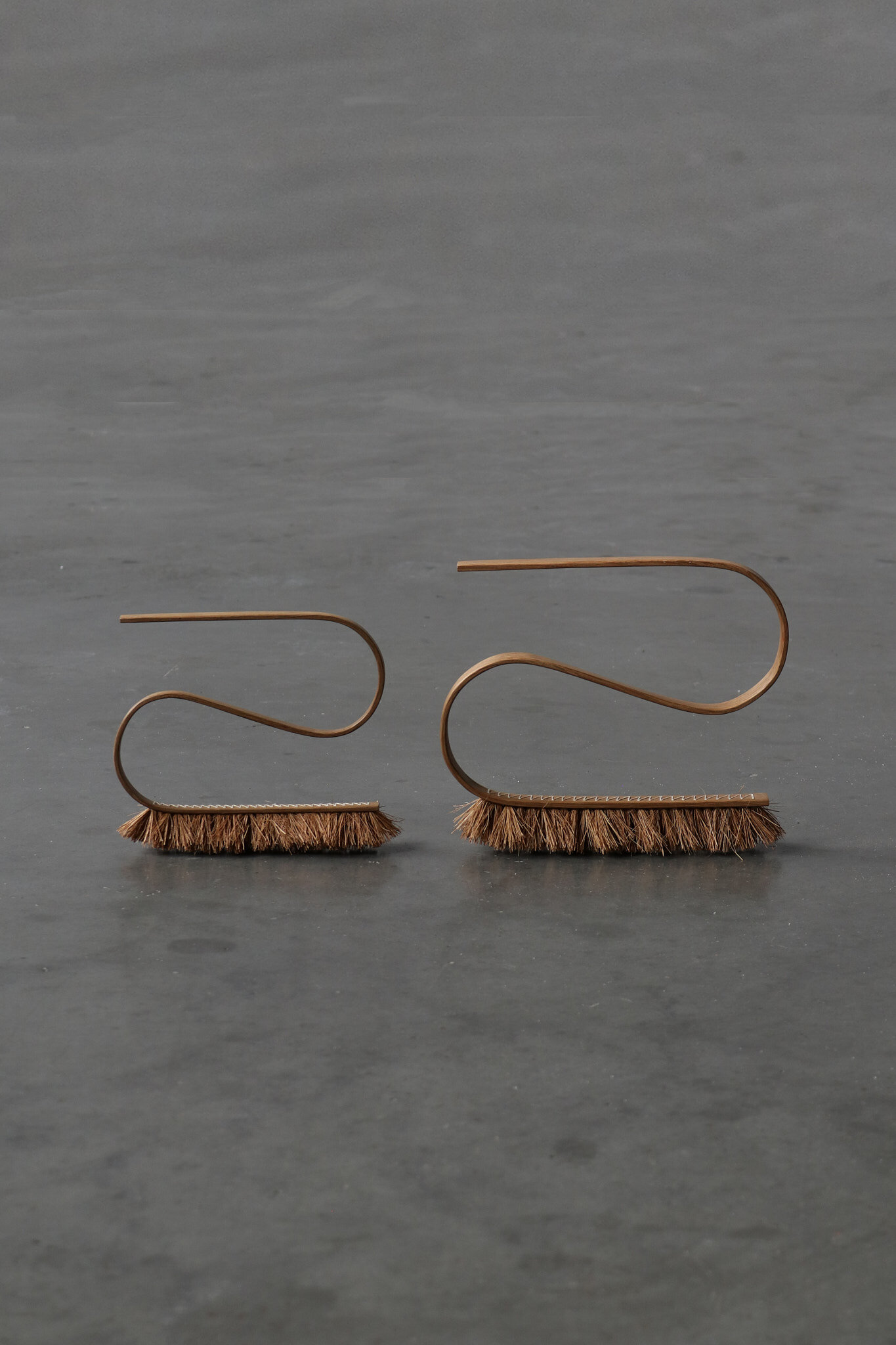
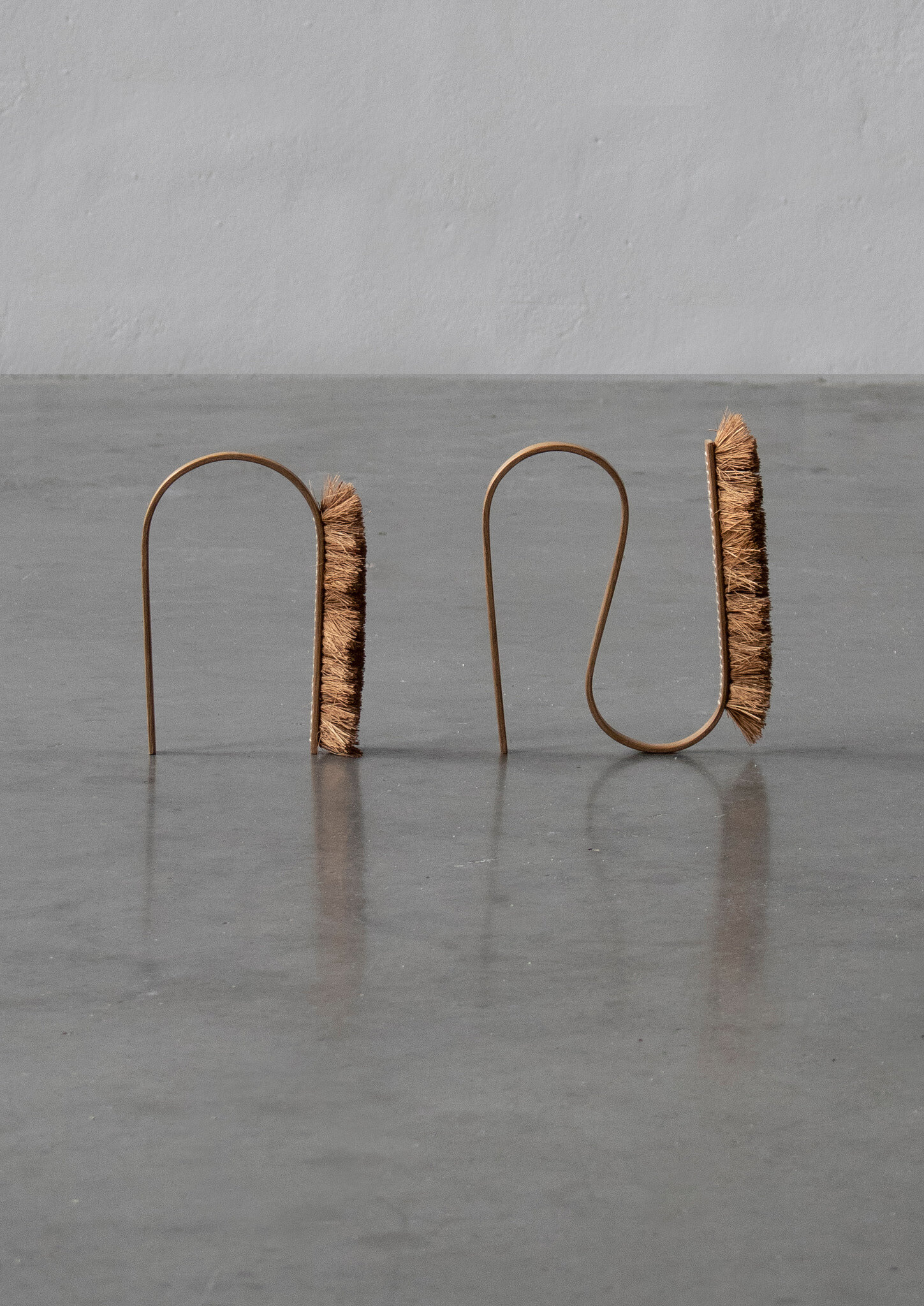
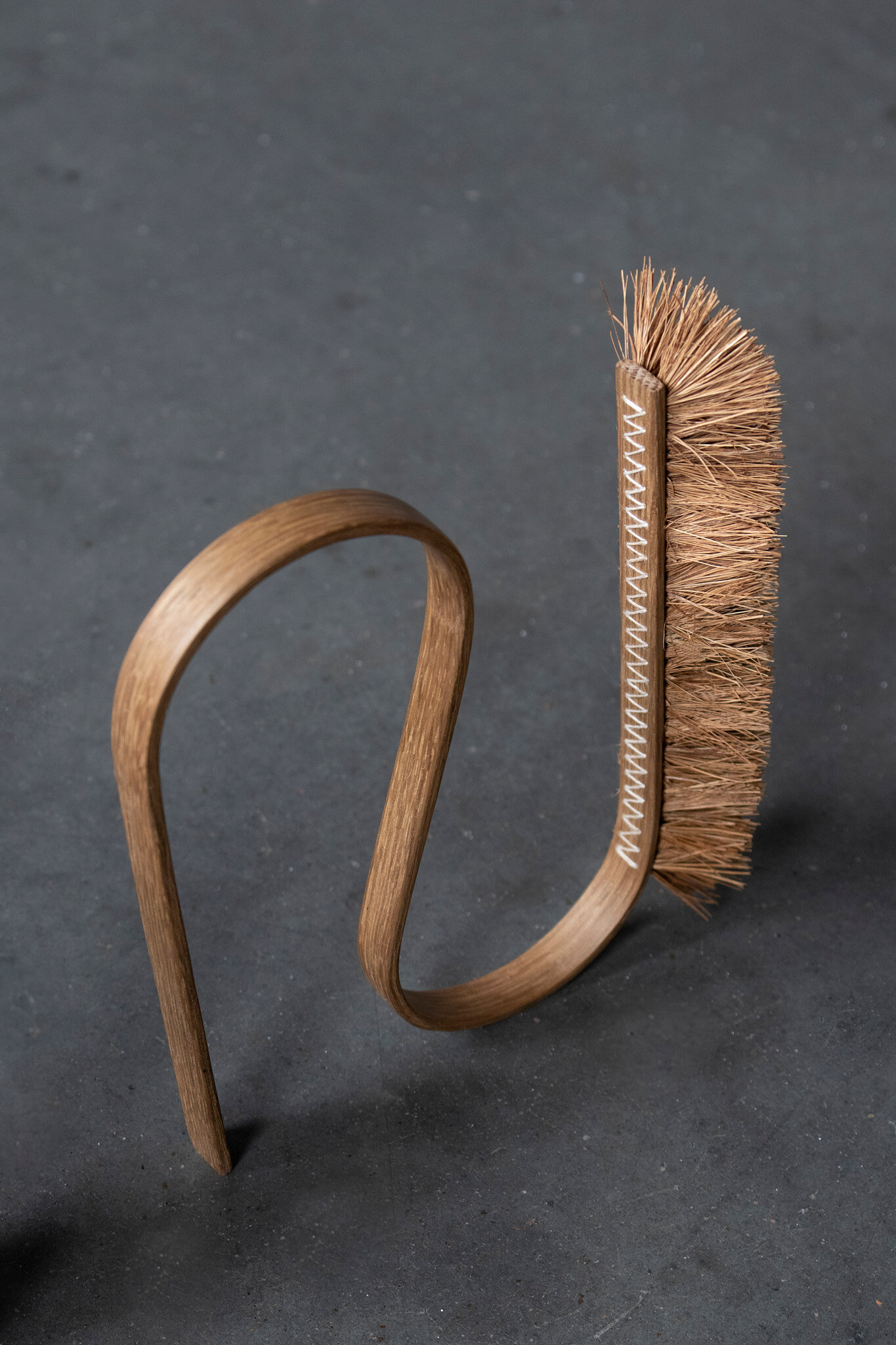
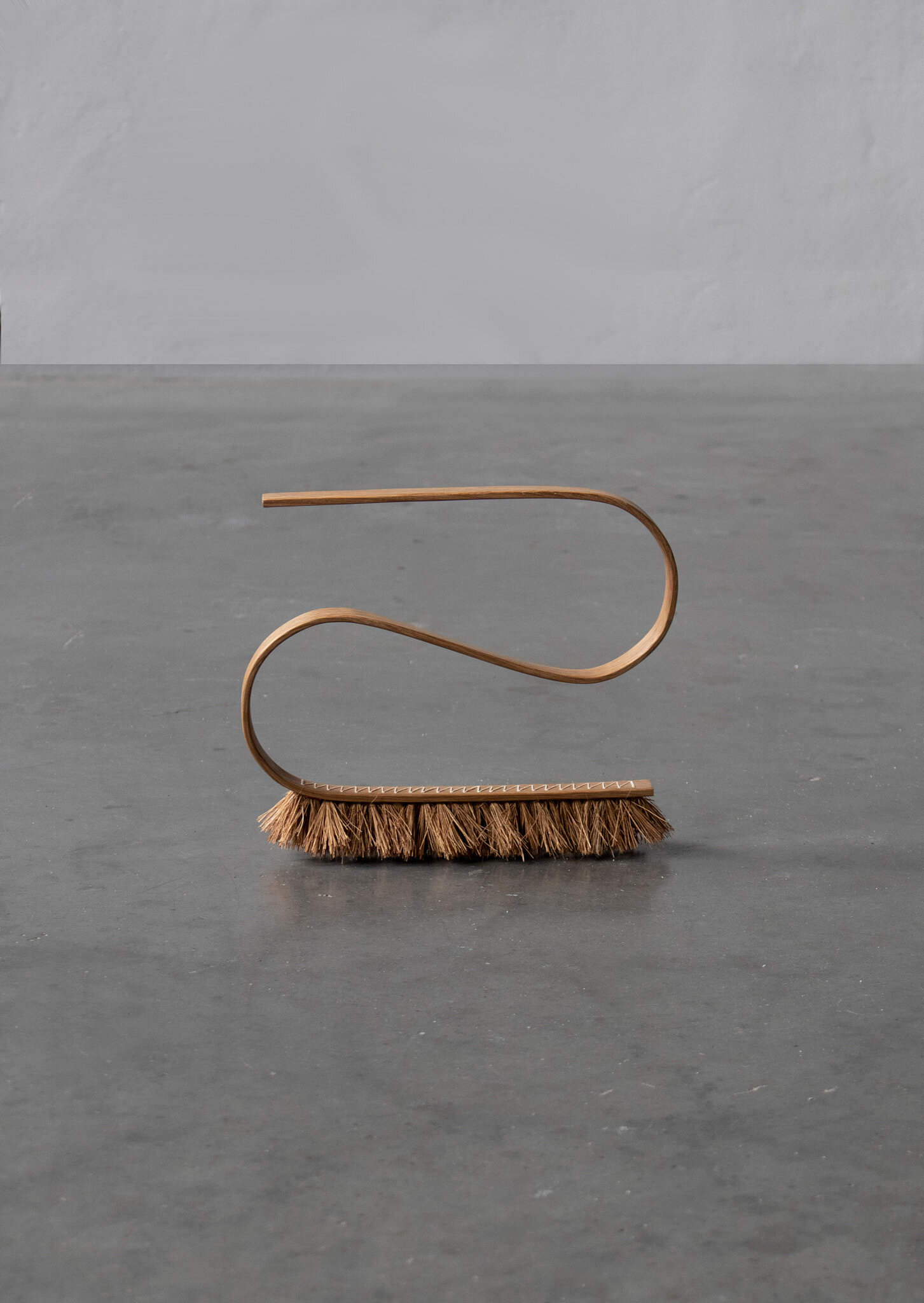
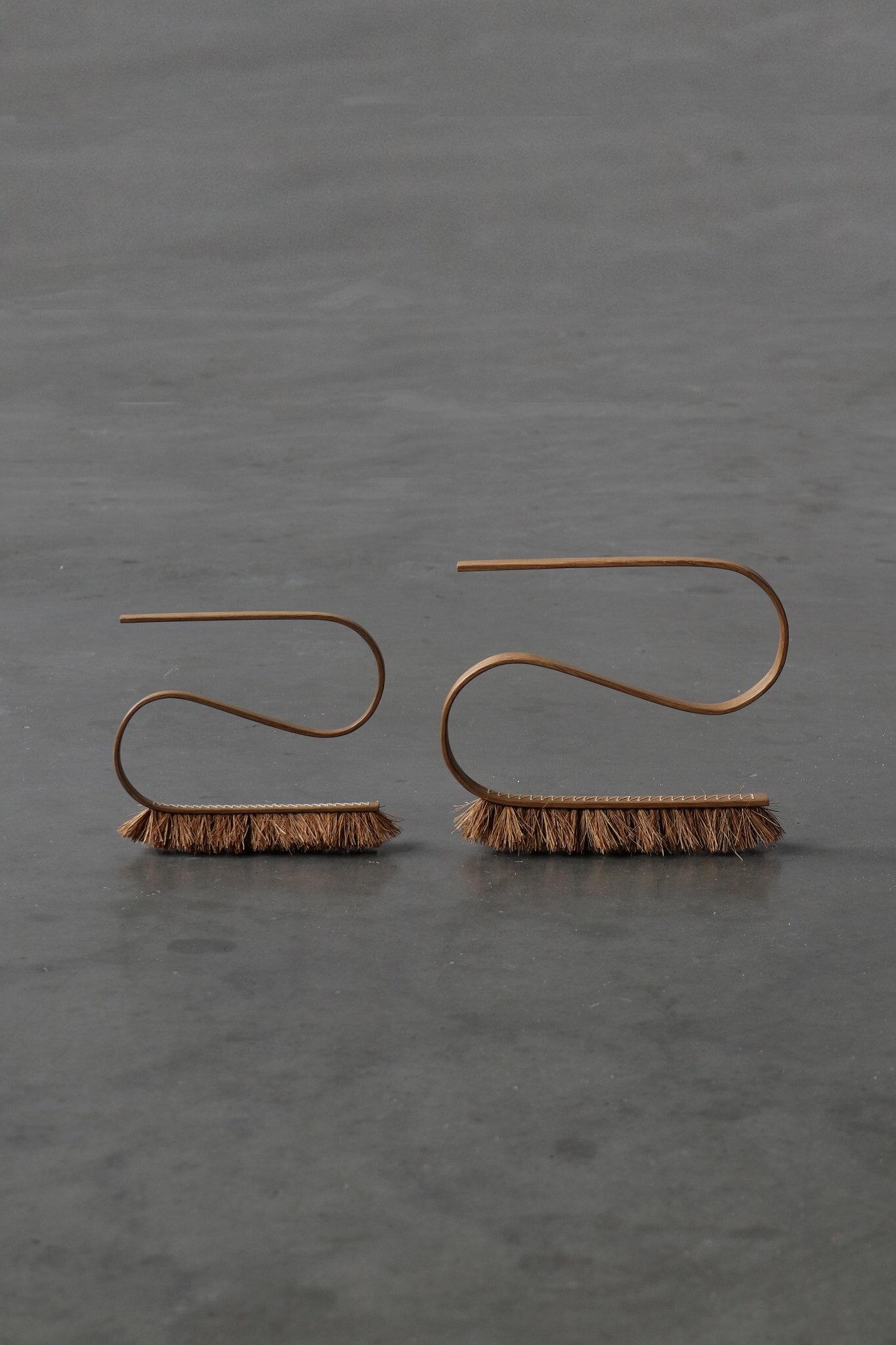
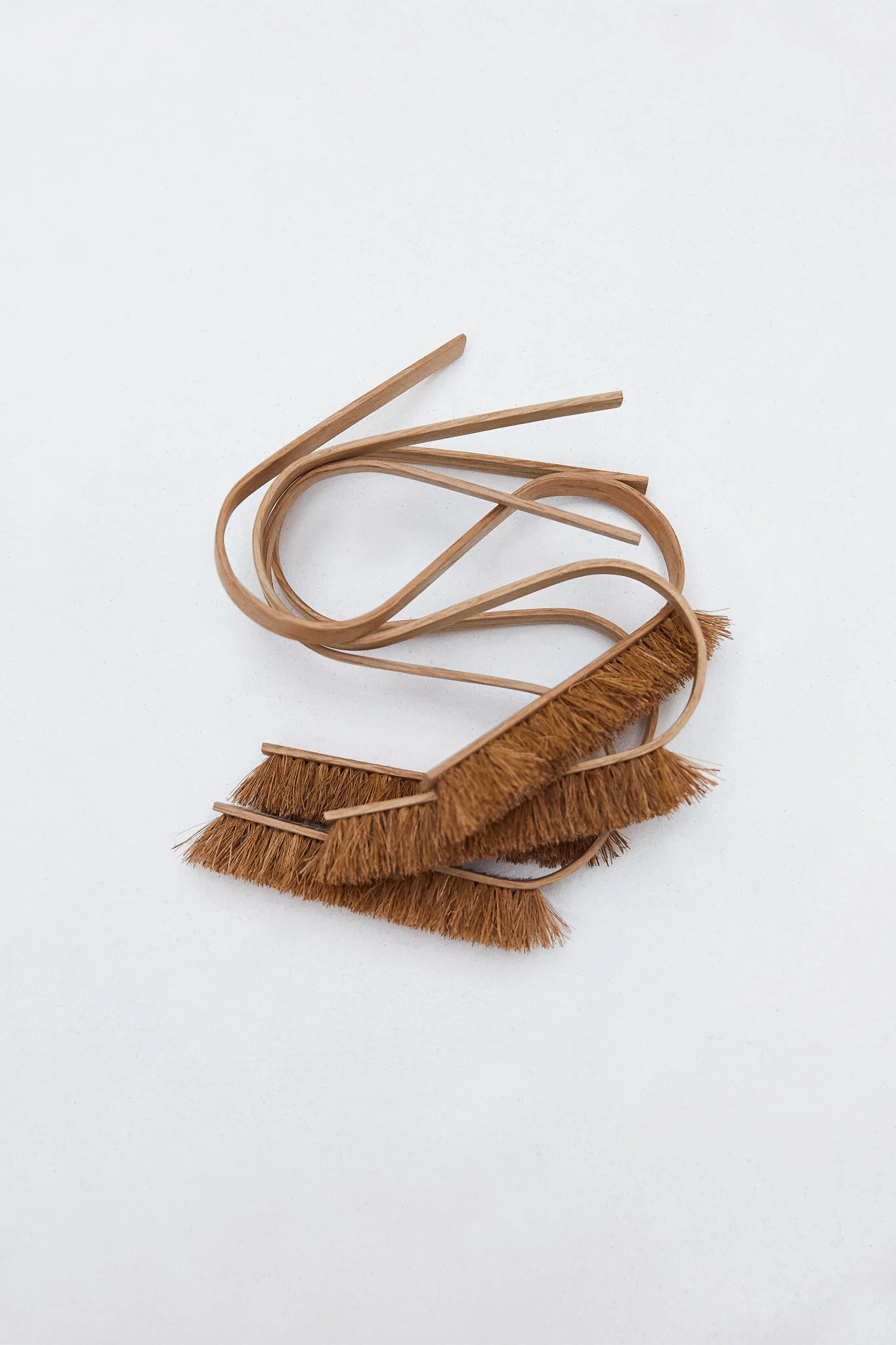
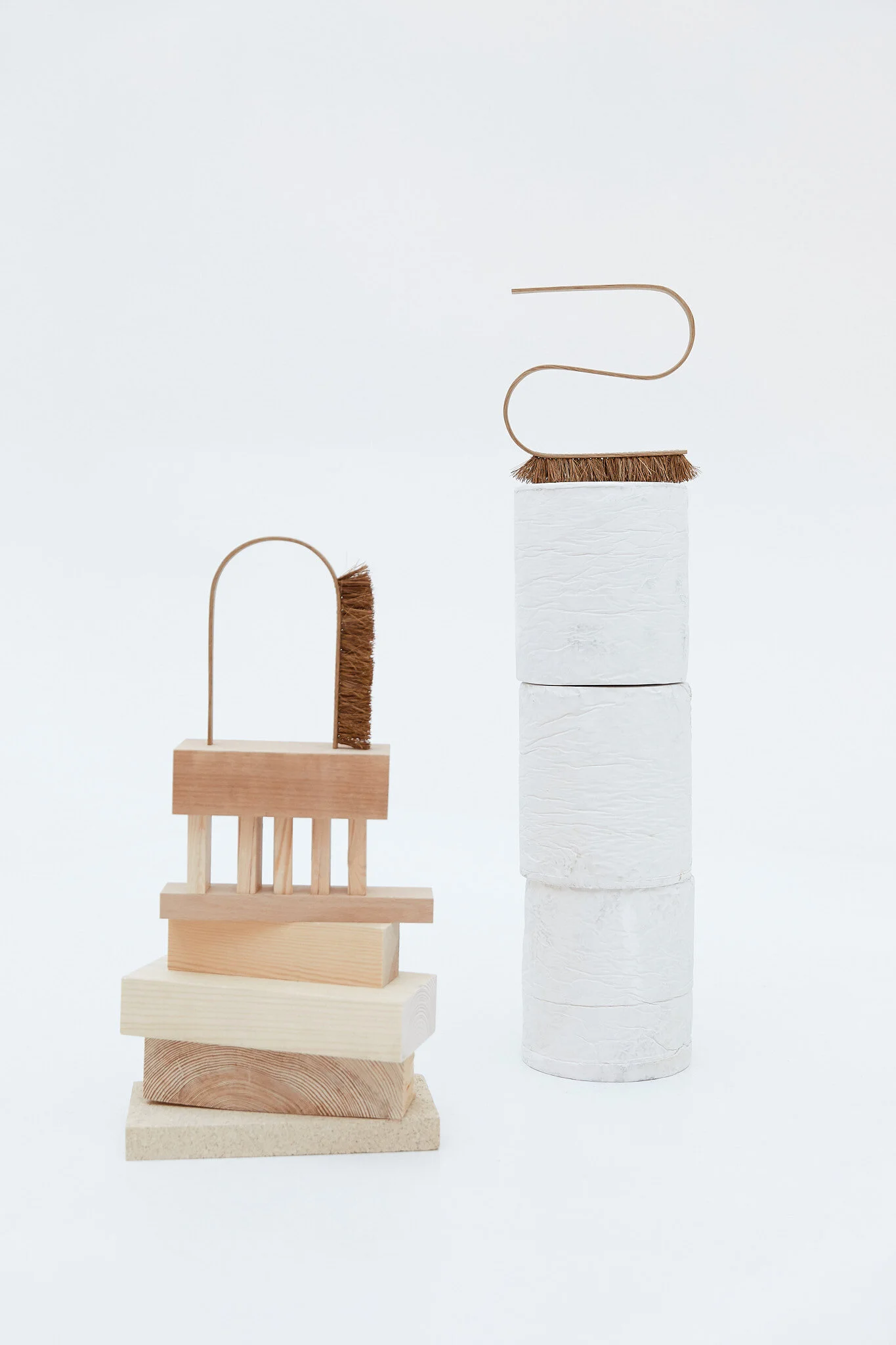
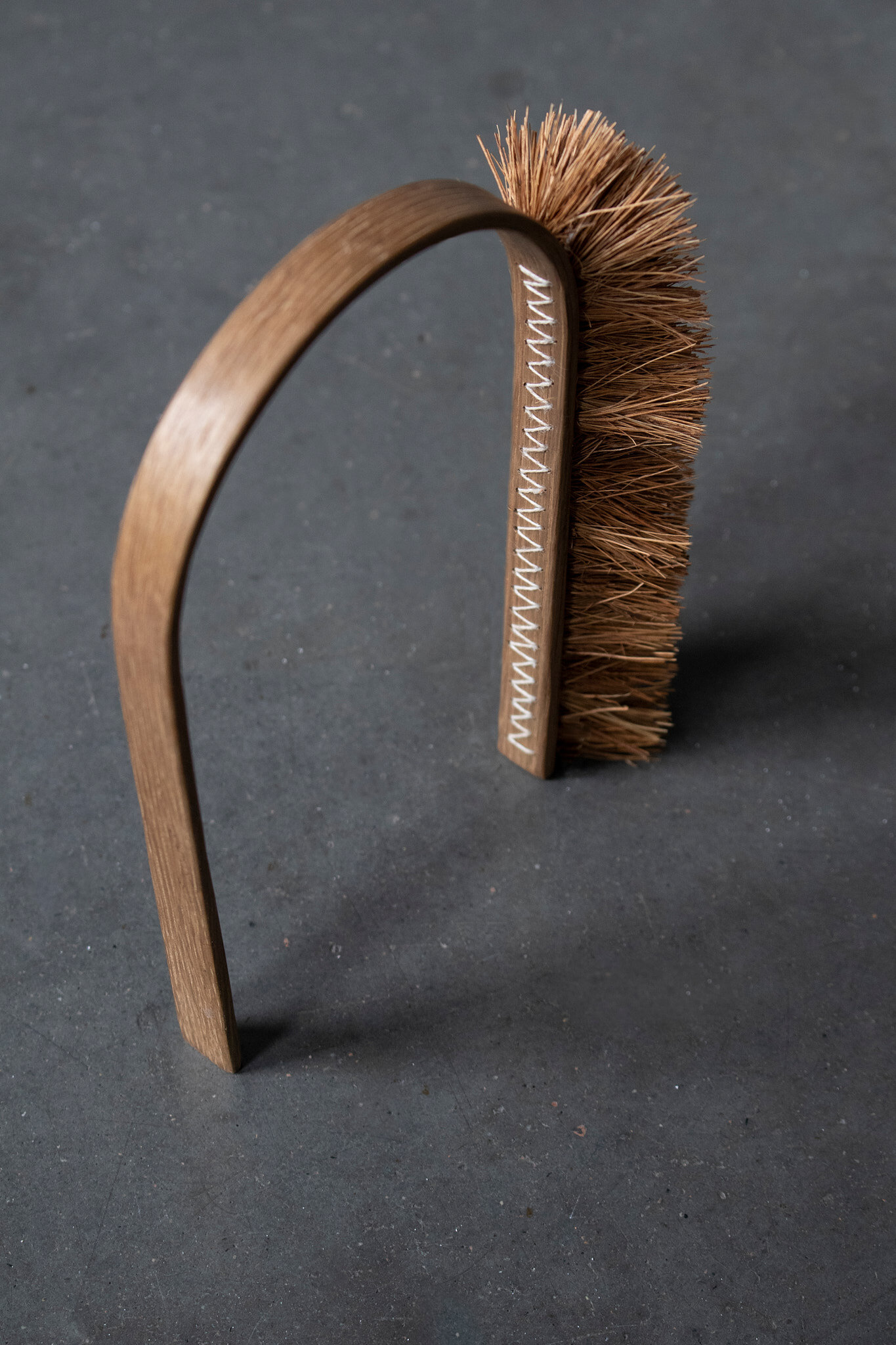
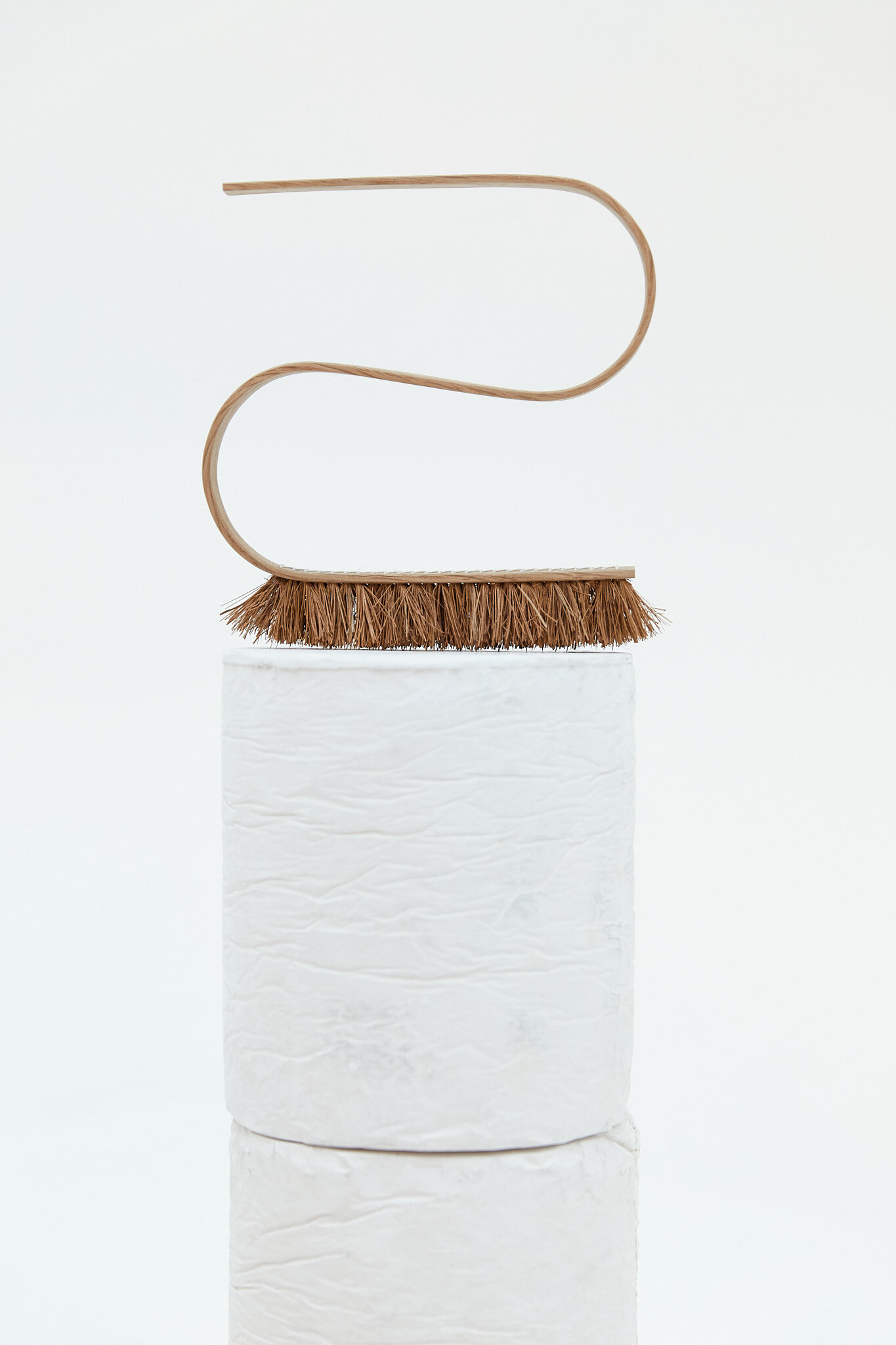
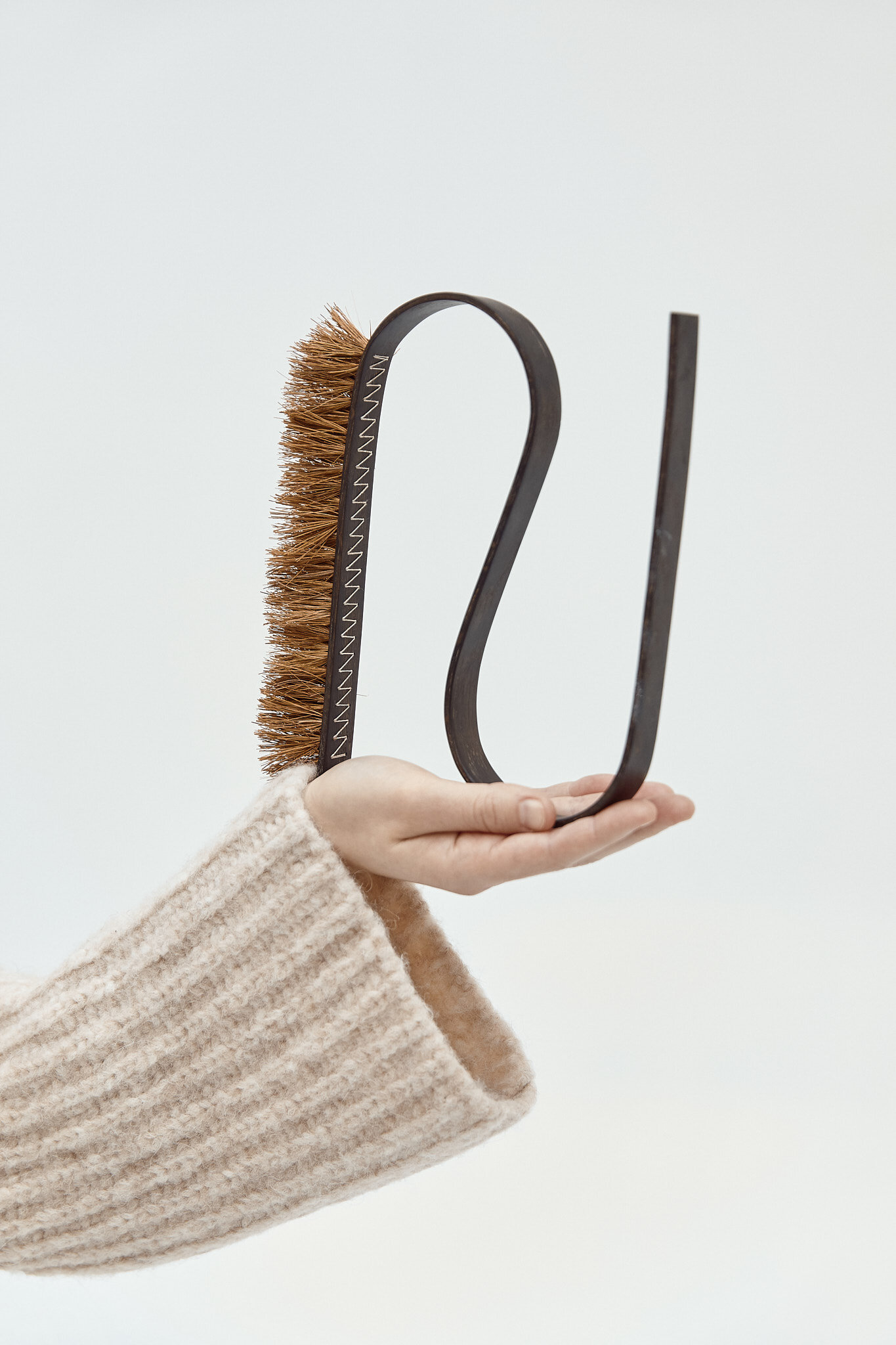

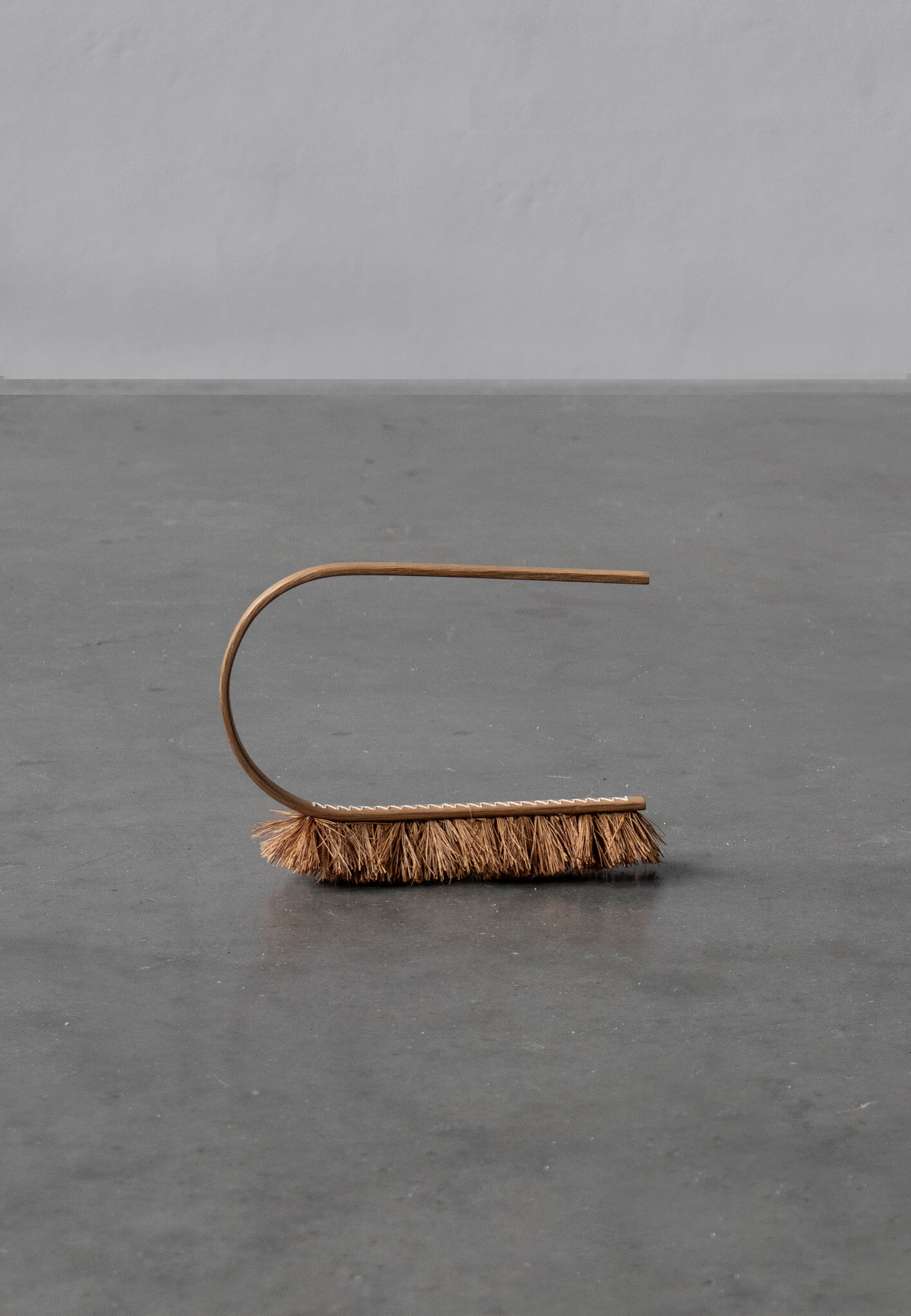

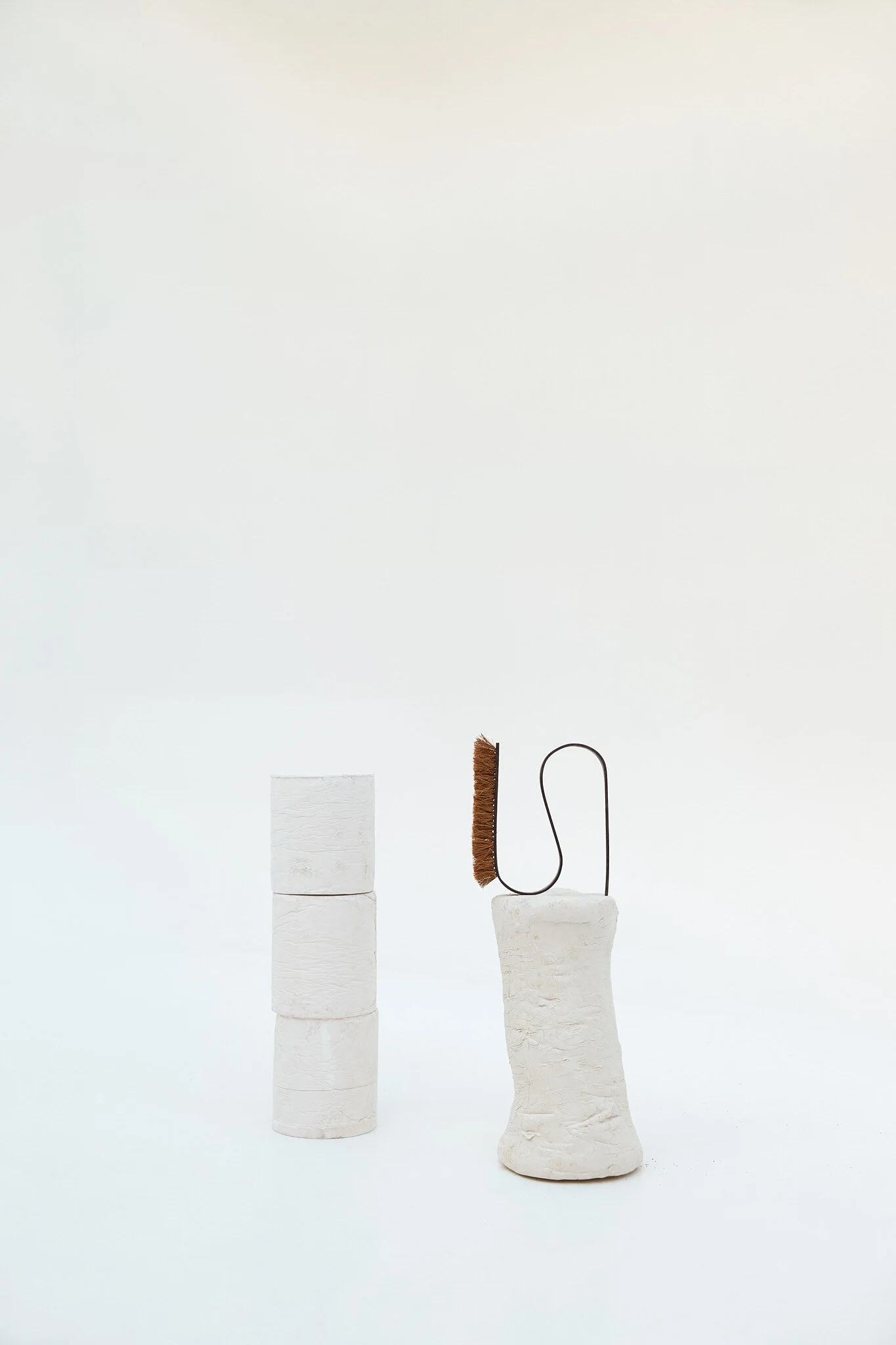
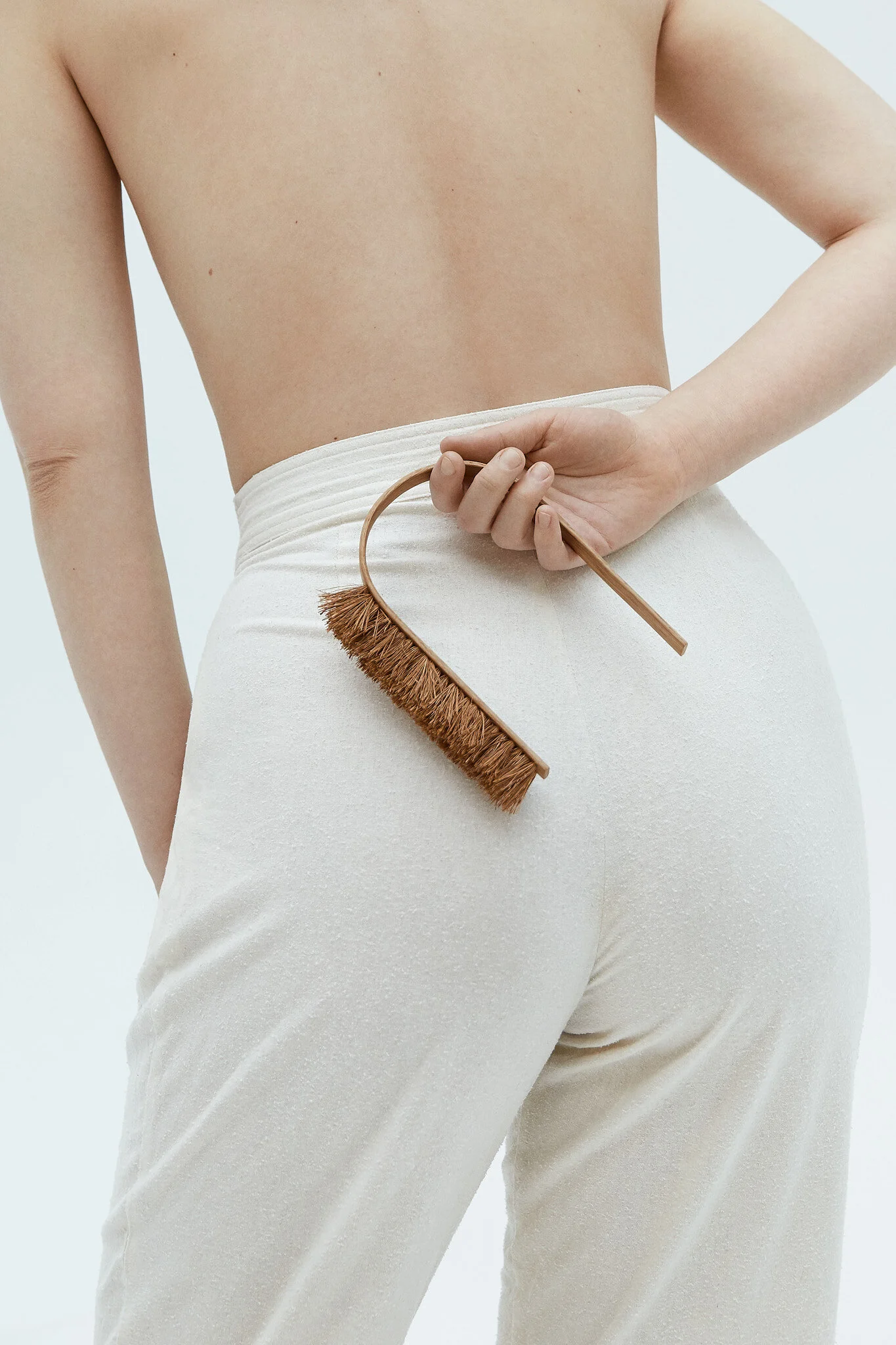
Technique/Info: The Bue series are part sculpture and part utilitarian, made to be enjoyed in and out of use; dancing the line of art and design for a slower, more connective way of living. Sculptural flowing, fluid forms of raw oak bend and fold through the technique of traditional steam bending, connecting us to a time old handcraft. Where once heated, the wood is malleable and supple ready to be formed by hand and take on shape. The Bue Brush series are a collection of table and dust brushes.
OOOLI
Vegetable tanned leather and Steel, 52cm x 34cm x 83cm, Made in Oslo
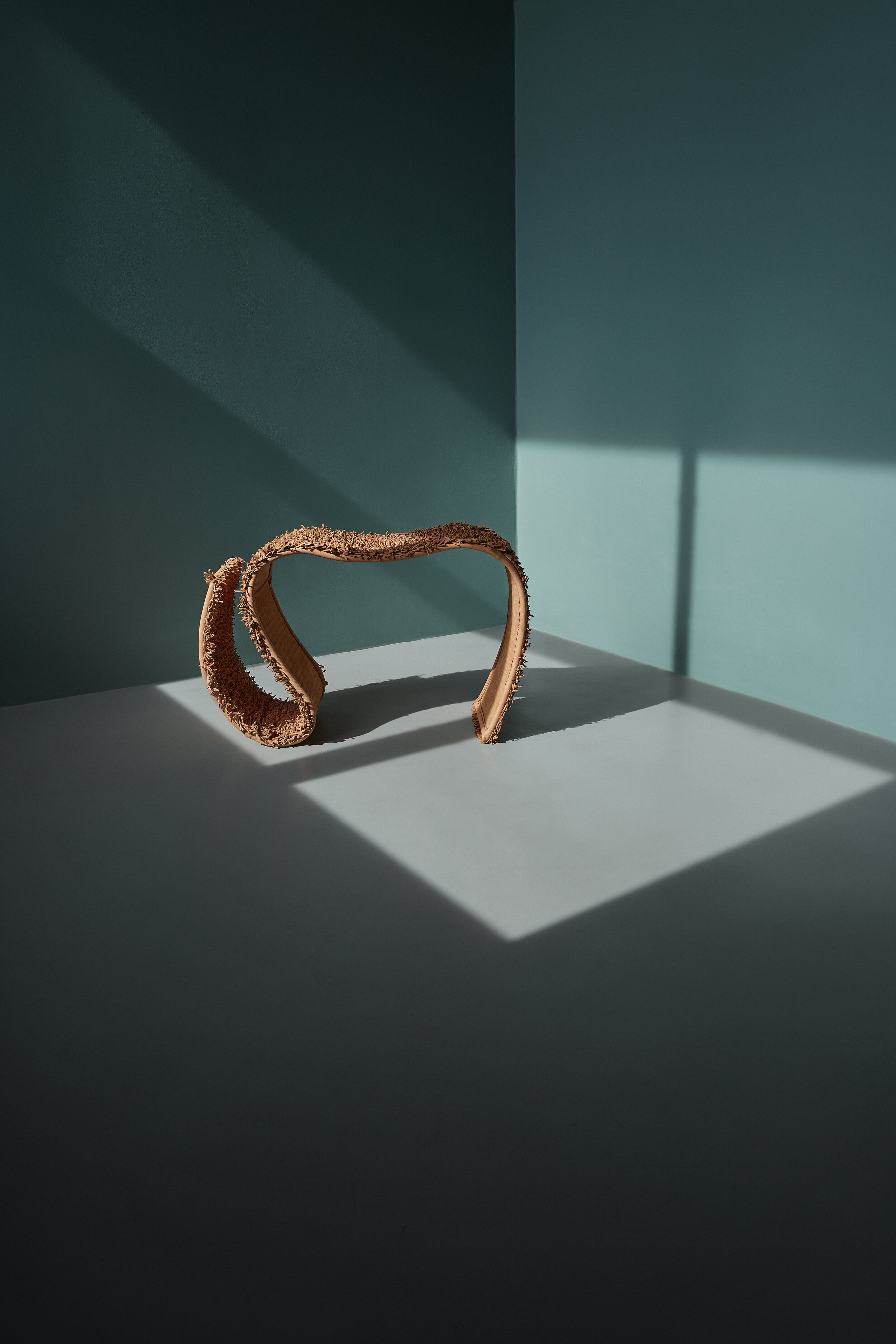
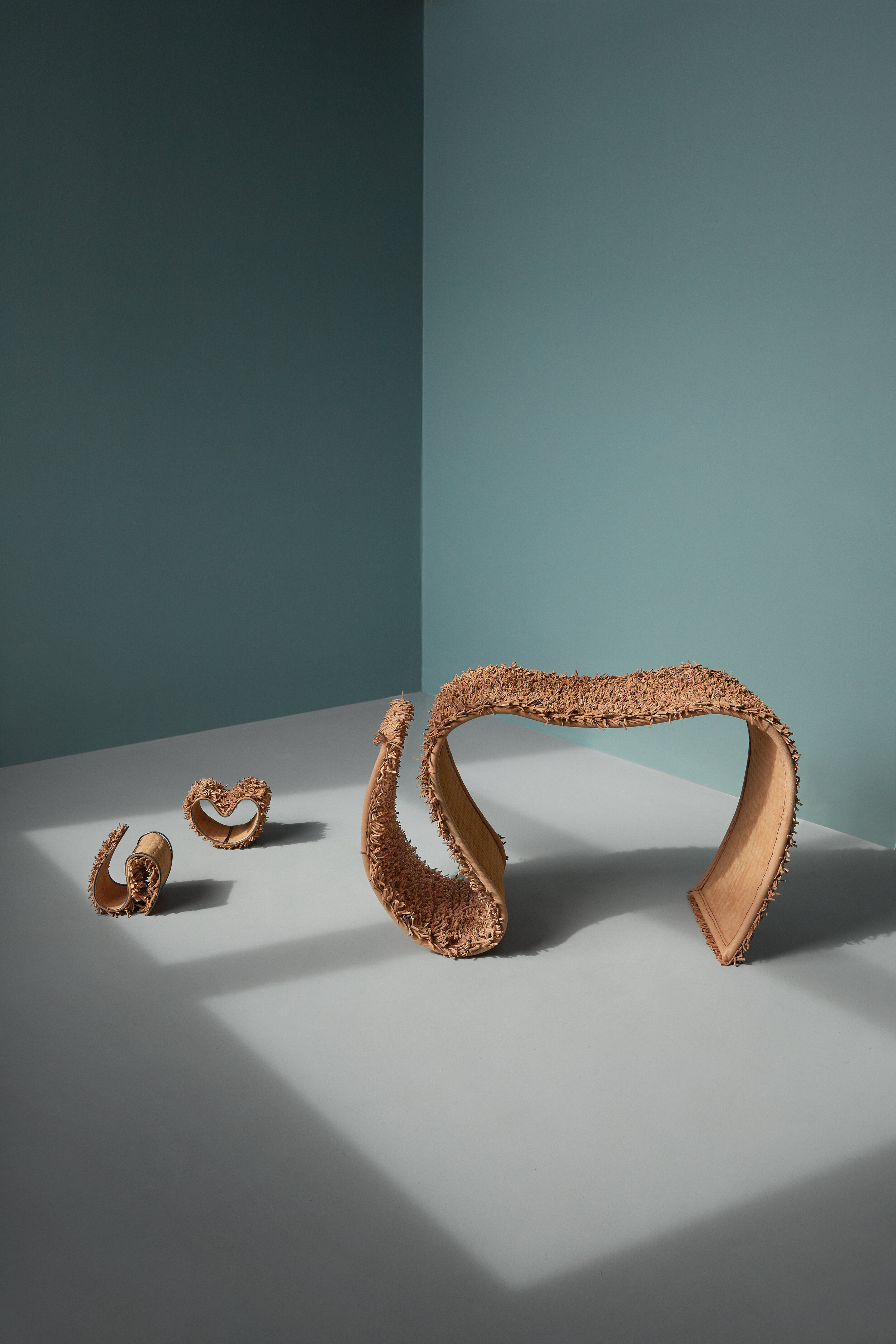
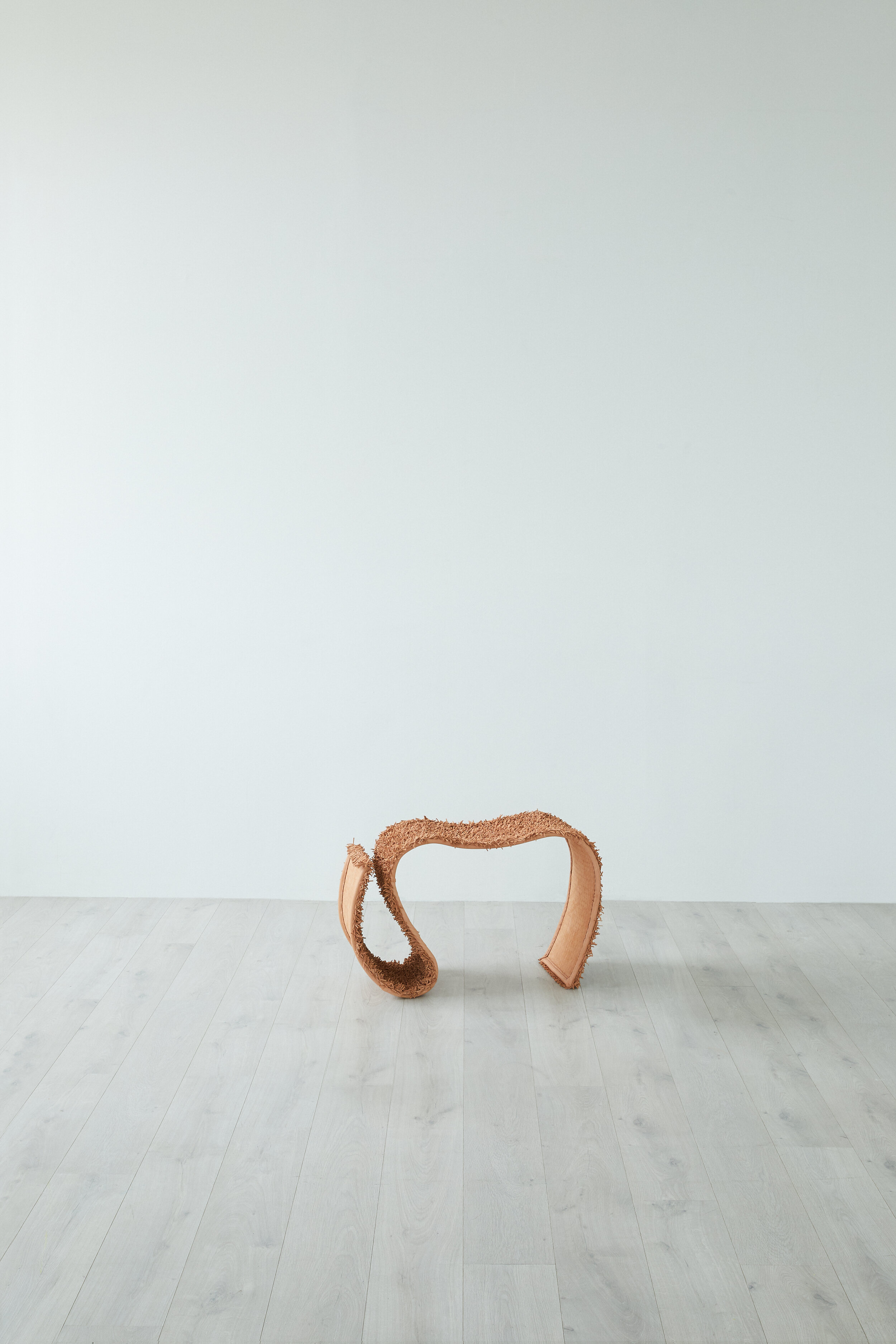


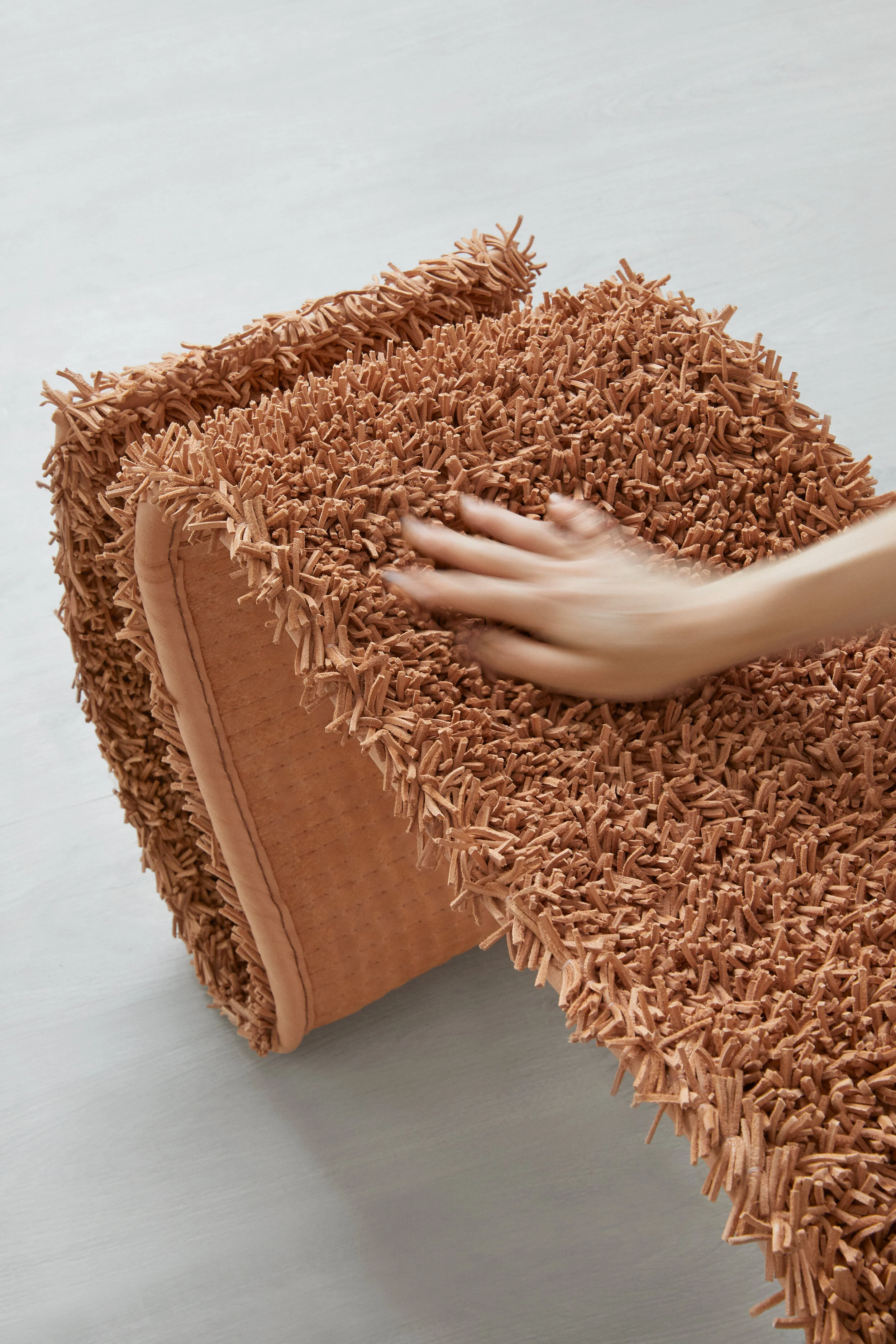
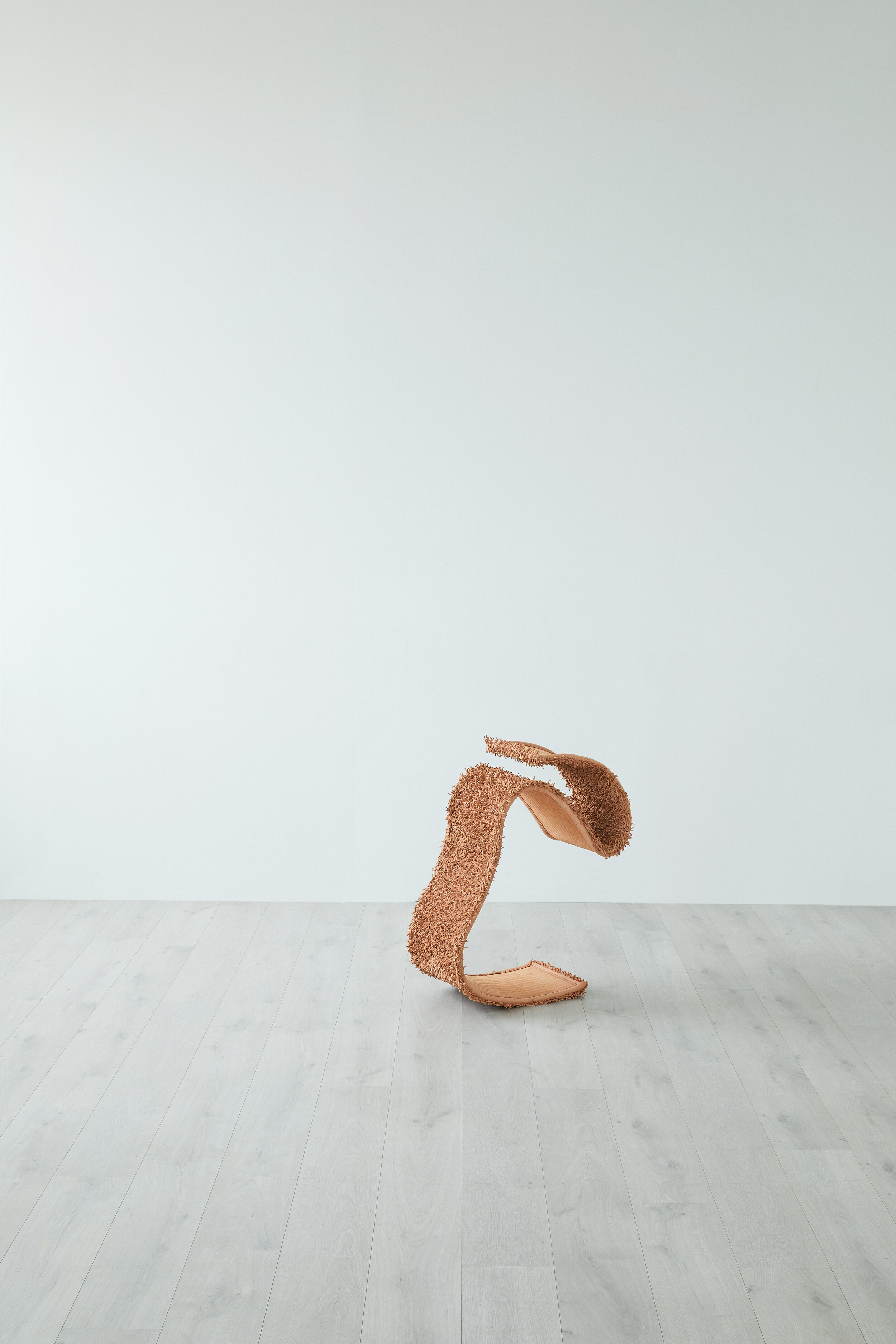
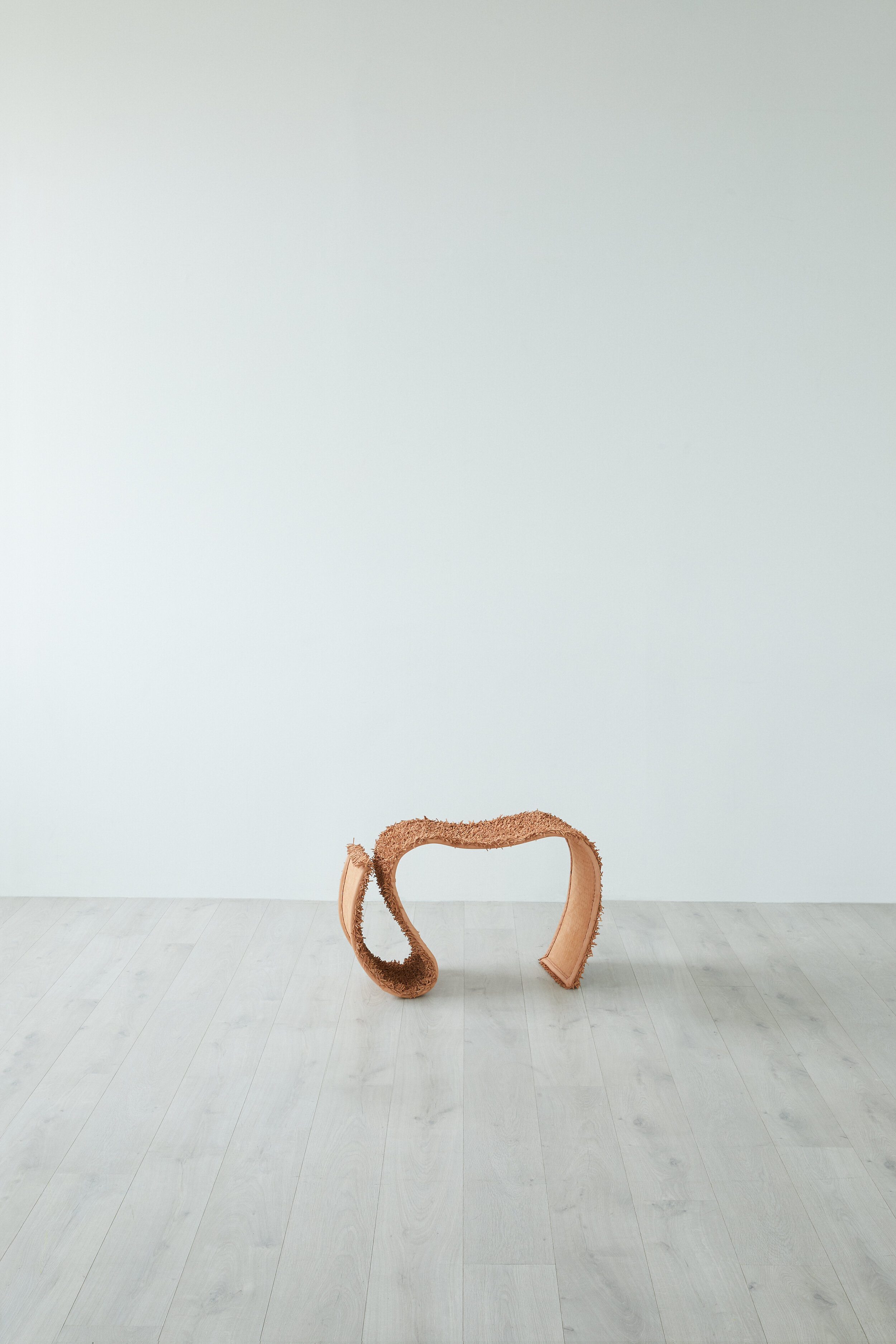
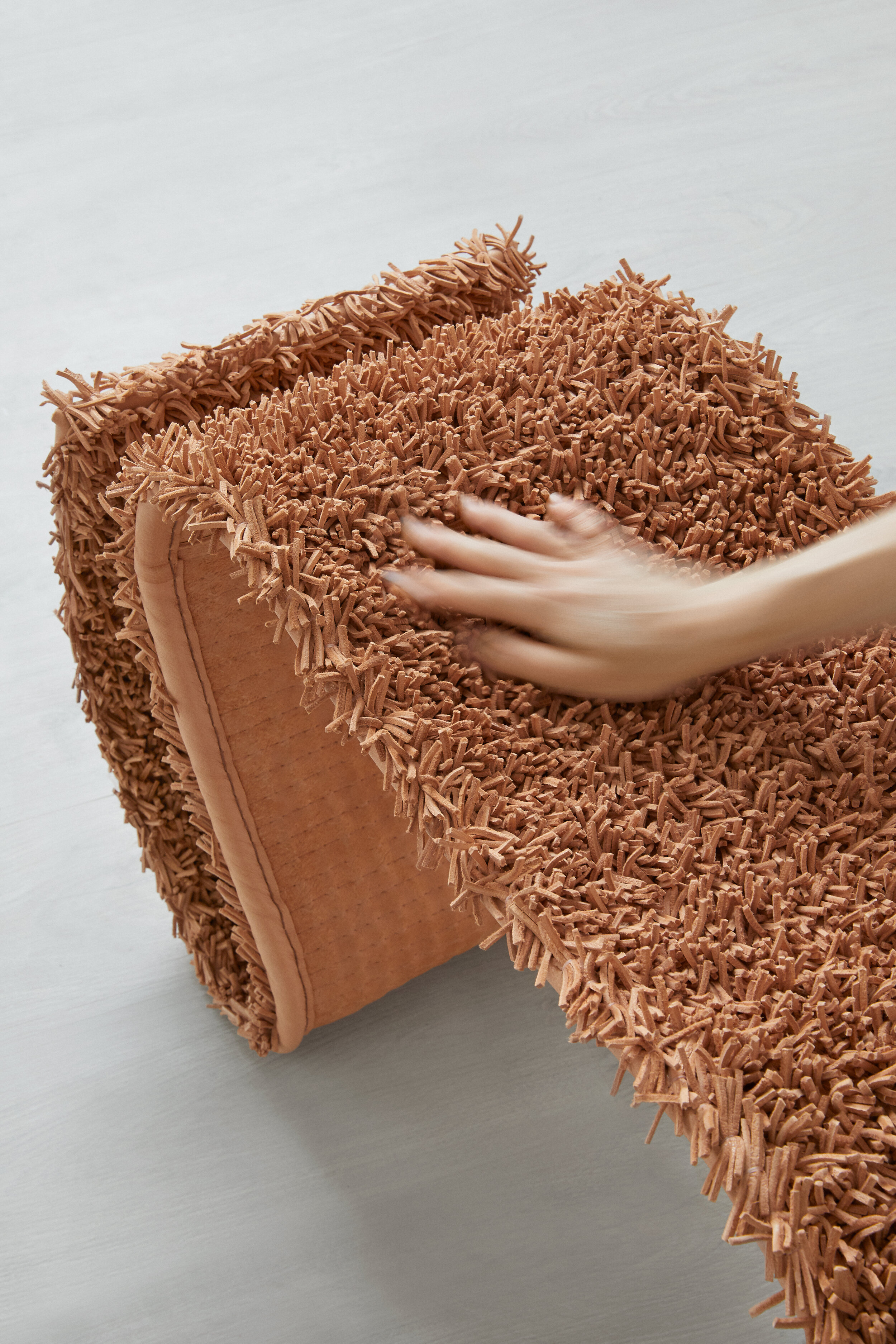
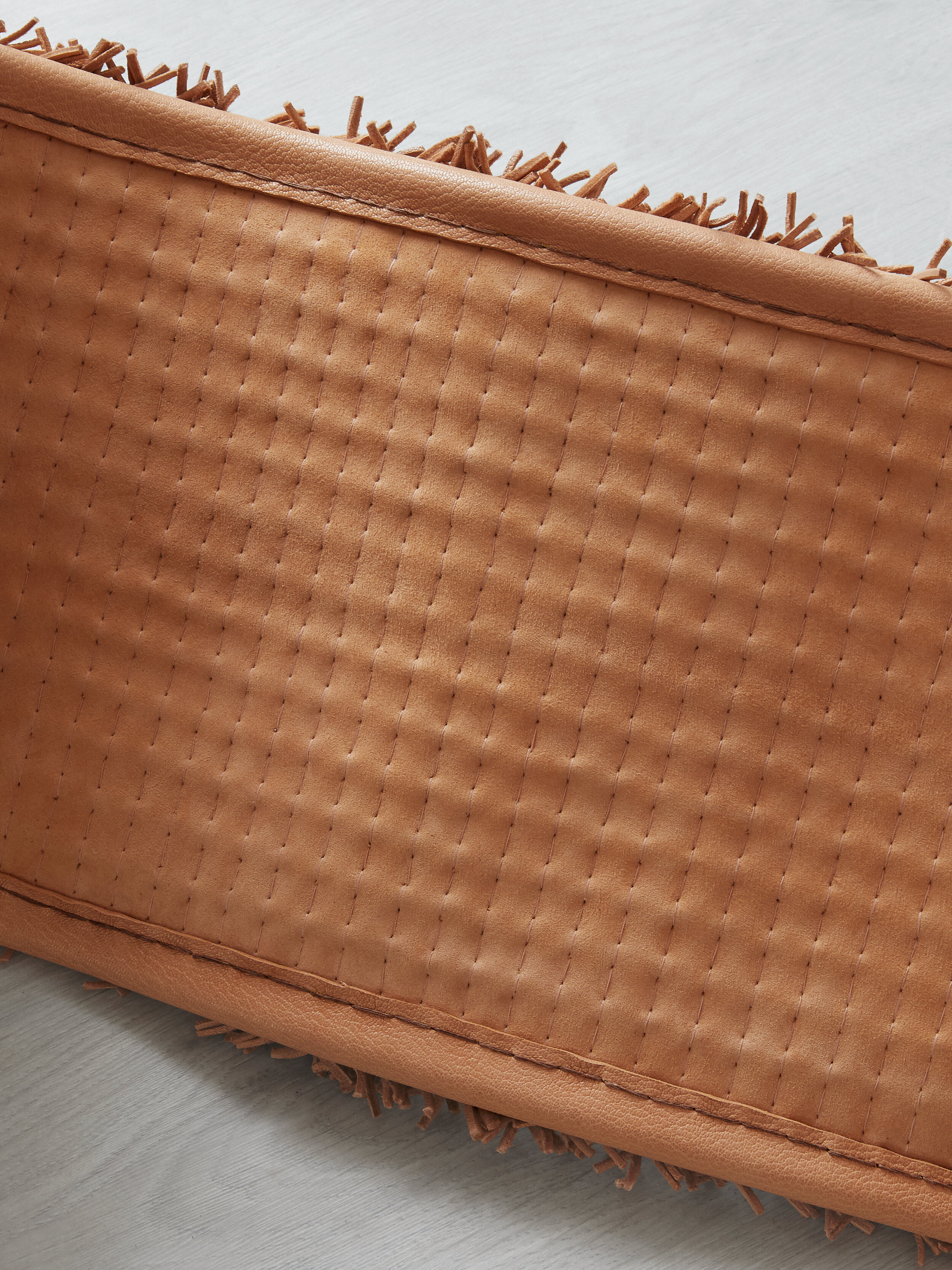
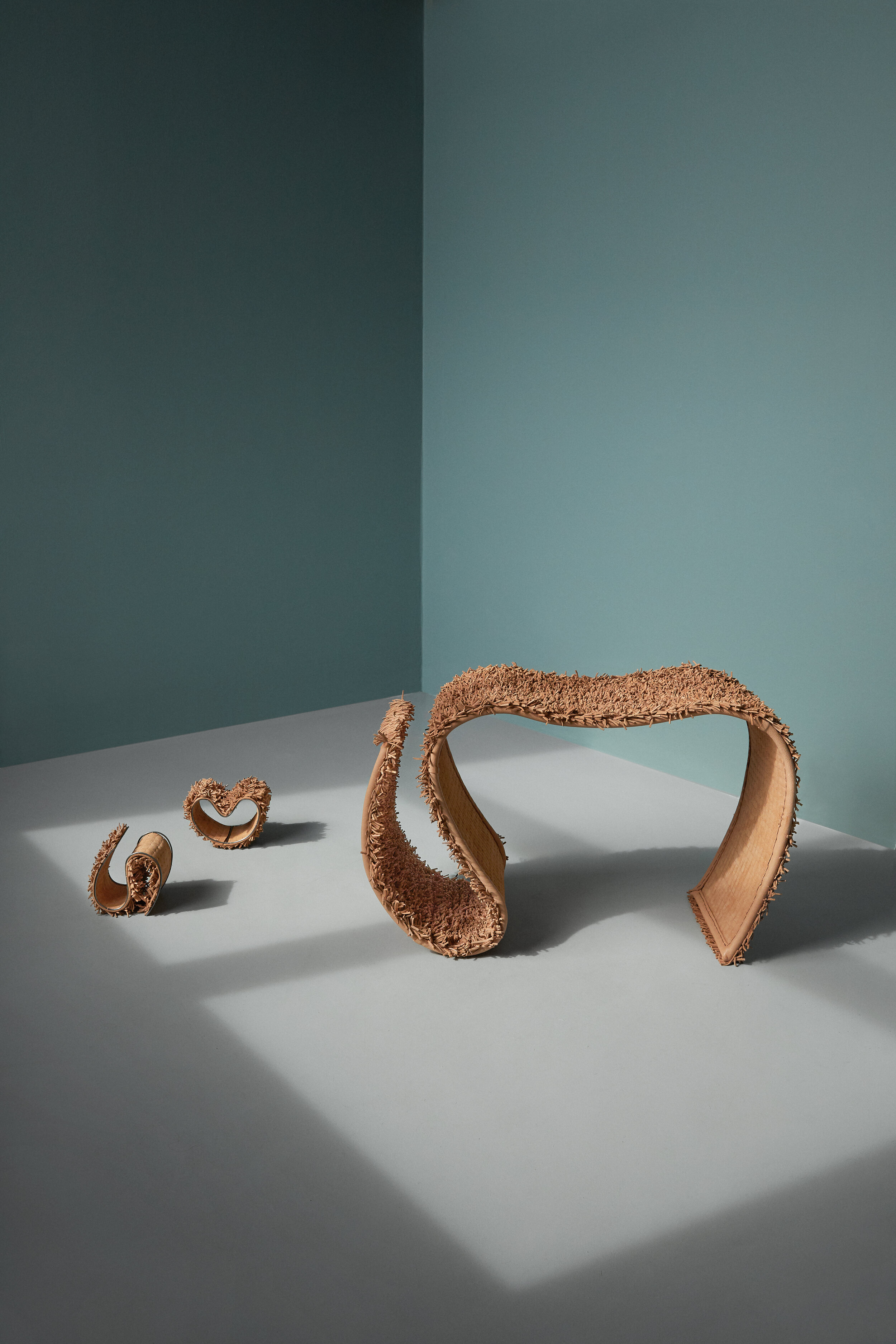
Oooli no.1 is a functional sitting sculpture whose form and tactual experience intend to intrigue and beckon one into it’s sitting embrace. Welcoming one to discover for oneself it’s forms and tactile nature as it brings you to a physical awareness of the moment with it’s mutual touch. The sitting sculpture Oooli no.1 is created by hand using 13,532 strips creating 2,255 bunches and using approximately 7,832 stitches.
Oooli no. 1 is from a collection of sculptural furniture and handheld objects of curiosity and play made of leather and steel utilising the entirety of the hide, off cuts and all, to create an intriguing, visceral, soft, and playful tactual experience. The objects dance the line of aesthetic and function merging a handcrafted quality and the visual experience of art with the utilitarian experience of design.
The materials used are made from renewable sources and chosen for their ability to mature and embrace time gracefully. Each pieces’ form has been forged by hand, hammer, and flame to create visually continuous forms intended to draw one in. The steel structure is finished in beeswax to protect it from future corrosion. The goat hide is supple and soft using a natural tanning process of bark and roots, sourced from a family tannery in southern Germany and prior to that the surrounding farms. The tactile surface endeavours to use the entirety of the hide and not just the large central forms commonly used when working with leather. Strip by strip each piece is carefully cut and sewn entirely by hand.